Choosing the Right Peristaltic Pump for Abrasive Fluids: Key Considerations for Industrial Applications
May 15,2025
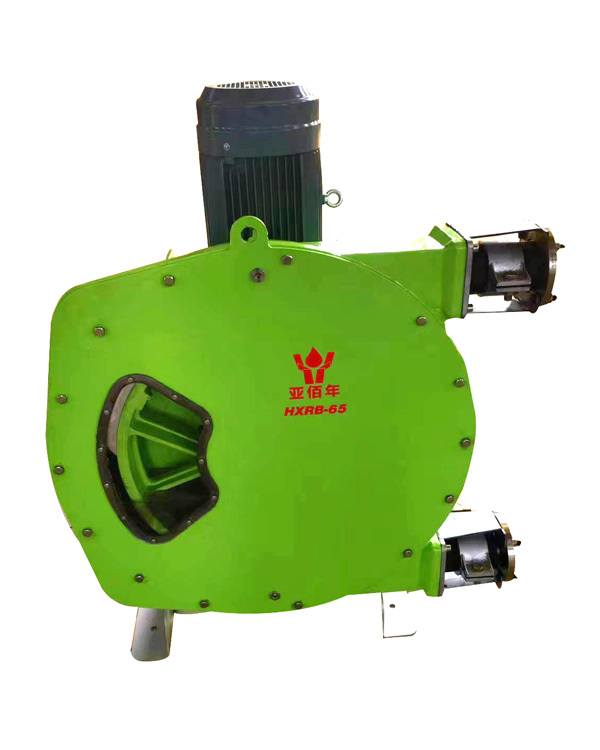
When dealing with abrasive fluids in industrial settings, the choice of pump can significantly impact operational performance and equipment lifespan. Peristaltic pumps are particularly well-suited for this purpose due to their unique design and functionality. Understanding the mechanics of peristaltic pumps and their advantages for abrasive fluid applications can lead to improved process efficiency and reduced downtime.
Peristaltic pumps operate by compressing a flexible tube, creating a vacuum that draws fluid into the pump. This action reduces wear and tear on the pump components, making it ideal for handling abrasive materials that can potentially damage other types of pumps. With minimal contact between the fluid and the pump's internal components, these pumps can effectively manage abrasive fluids, including slurries and viscous materials.
One of the key factors to consider when selecting a peristaltic pump for abrasive fluids is the material of the tubing. The tubing material must be robust enough to withstand the abrasive nature of the fluid being pumped. Common options include reinforced rubber or thermoplastic elastomers, which offer higher resistance to wear and extended service life. Additionally, it is crucial to choose a pump with adjustable flow rates to accommodate varying process requirements, ensuring optimal performance.
Another important consideration is the pump's ability to handle solids within the fluid. Peristaltic pumps can efficiently handle fluids with suspended solids, but understanding the size and concentration of these solids is vital to ensure the pump operates effectively without clogging. Incorporating a filtration system upstream can further mitigate risks and enhance performance, allowing for consistent flow rates.
Maintenance is another aspect that cannot be overlooked. Since peristaltic pumps have fewer moving parts, they generally require less maintenance compared to other pump types. However, regular inspection of the tubing for wear and tear is essential, as the tubing is the primary component exposed to the abrasive fluid. Proper maintenance practices can extend the lifespan of the pump and prevent unexpected failures.
In conclusion, when selecting a peristaltic pump for abrasive fluids, it is essential to consider the tubing material, pump capacity, and maintenance requirements. By understanding these factors, industrial professionals can make informed choices that enhance operational efficiency, reduce downtime, and ultimately save costs. The robustness of peristaltic pumps makes them a reliable option for various applications involving abrasive materials, ensuring long-term performance and reliability in demanding environments.
Peristaltic pumps operate by compressing a flexible tube, creating a vacuum that draws fluid into the pump. This action reduces wear and tear on the pump components, making it ideal for handling abrasive materials that can potentially damage other types of pumps. With minimal contact between the fluid and the pump's internal components, these pumps can effectively manage abrasive fluids, including slurries and viscous materials.
One of the key factors to consider when selecting a peristaltic pump for abrasive fluids is the material of the tubing. The tubing material must be robust enough to withstand the abrasive nature of the fluid being pumped. Common options include reinforced rubber or thermoplastic elastomers, which offer higher resistance to wear and extended service life. Additionally, it is crucial to choose a pump with adjustable flow rates to accommodate varying process requirements, ensuring optimal performance.
Another important consideration is the pump's ability to handle solids within the fluid. Peristaltic pumps can efficiently handle fluids with suspended solids, but understanding the size and concentration of these solids is vital to ensure the pump operates effectively without clogging. Incorporating a filtration system upstream can further mitigate risks and enhance performance, allowing for consistent flow rates.
Maintenance is another aspect that cannot be overlooked. Since peristaltic pumps have fewer moving parts, they generally require less maintenance compared to other pump types. However, regular inspection of the tubing for wear and tear is essential, as the tubing is the primary component exposed to the abrasive fluid. Proper maintenance practices can extend the lifespan of the pump and prevent unexpected failures.
In conclusion, when selecting a peristaltic pump for abrasive fluids, it is essential to consider the tubing material, pump capacity, and maintenance requirements. By understanding these factors, industrial professionals can make informed choices that enhance operational efficiency, reduce downtime, and ultimately save costs. The robustness of peristaltic pumps makes them a reliable option for various applications involving abrasive materials, ensuring long-term performance and reliability in demanding environments.
Contact Us
E-mail :
sales@yaquanpump.com
service@yaquanpump.com
Phone/WhatsApp:
+44 7301702546
+63 9452052801
Address:
Room B208, Building 2, North Hongqiao Songri Center, No.215 Gaochao Road, Jiading District, Shanghai